PC interfaces and adapters for Fieldbus connection
Aspiration: To link data worlds
Expertise: USB-to-CAN interfaces
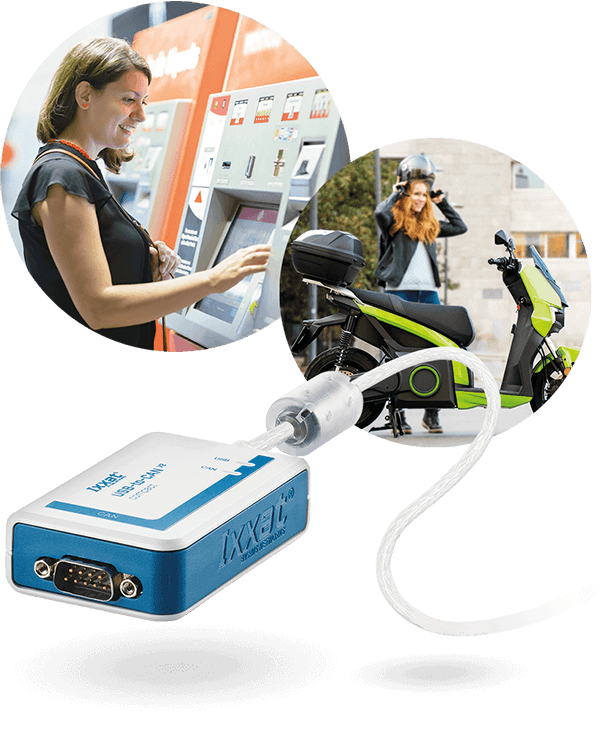
All variants at a glance

USB-to-CAN conversion: Industrial applications at a glance
USB-CAN adapters for start-up, diagnosis, and maintenance
Testing battery systems at EV workshops via CAN network
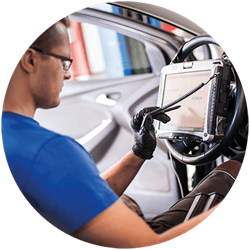
Testing battery systems in electric vehicles is a core task of automotive workshops specialising in electric mobility. Numerous parameters such as state of charge or cell temperature must be transferred via the USB interface from the CAN network of the BMS to the workshop PC. This connection can be set up fast and conveniently as a plug-and-play solution using a USB-to-CAN converter.
CAN diagnosis of electric scooters in workshops
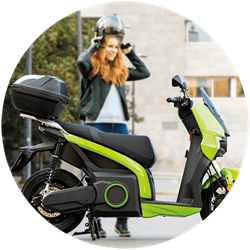
Reading out fault memories in leisure watercraft using USB-to-CAN adapters
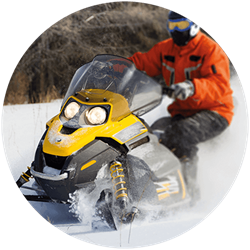
Diagnosis and maintenance of air-conditioning control units in passenger cars using CAN adapters
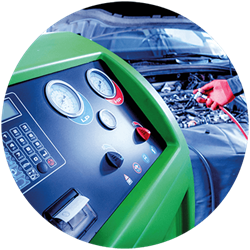
USB-CAN adapters for controller-based process control
Process control of sensors and actuators in medical microscopes
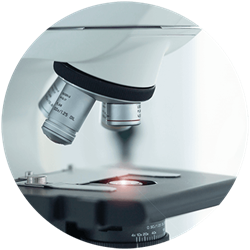
CAN conversion in automated PCR systems for research, medical technology, or biotechnology
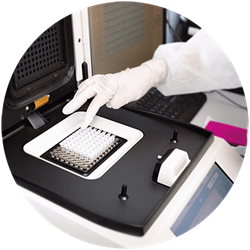
Monitoring control processes in robust industrial PCs for construction machinery
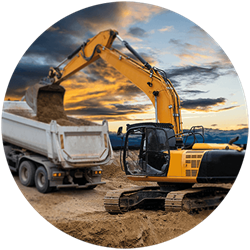
Fieldbus control of ticketing machines with CAN communication
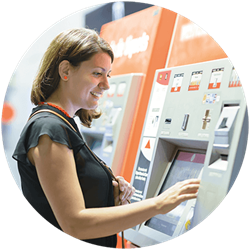
Technical data and advantages
USB-to-CAN V2 compact: Control CAN networks quickly and easily
Figures for CAN professionals:
Technical data
- PC bus interface: USB 2.0, Hi-Speed
- CAN controller: Internal CAN 2.0 A/B
- CAN baud rates from 10 to 1000 kbit/s
- LIN protocol V1.3 and V2.0
- LIN baud rate: maximum 20 kBaud
- Microcontroller 32-bit
- Galvanic isolation 1000 VDC / 1 sec., 500 VAC / 1 min.
- Temperature range between -20 and +70 °C
- Power supply: 5 V, maximum 300 mA via USB connector (standby mode 30 mA)
User benefits:
USB-to-CAN advantages
- Multisystem compatibility with Windows, Linux, real-time operating system thanks to multicompatible VCI, ECI, and SocketCAN driver packages
- Wide-ranging protocol support: High-speed CAN, low-speed CAN (as per ISO 11898-3), CAN FD, and LIN
- Freedom of use thanks to flexibly selectable D-SUB9 and RJ45 connectors or direct integration
- High stability during industrial use: Permanently integrated USB cable
- Bulk variants for sustainable mass applications
- Compact designs: Desktop versions (80 x 50 x 22 mm), embedded cards (67 x 40 x 18 mm), plug-in versions (67.5 x 40 x 9.2 mm)
- Robust, durable plastic housing made of recyclable and industry-tested ABS plastic
Build innovative machines faster without costly prototyping with Efficient Motion Control.
With Effective Motion Control, machine builders can easily overcome major challenges and enable faster time-to-market, increased functionality, resolve complex system requirements, and demands for safety and sustainability.
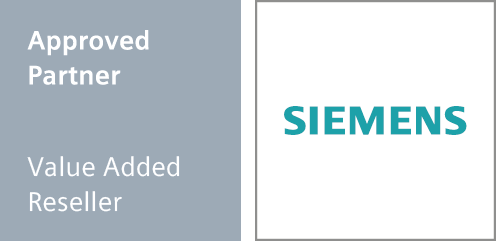
We are Siemens trusted and approved distribution partner.
As a Value Added Reseller in Siemens’ Approved Partner network, Parmley Graham is a proven supplier of a wide range of quality products in the UK and globally.
Find out more how this will benefit you or check Siemens Configurator.