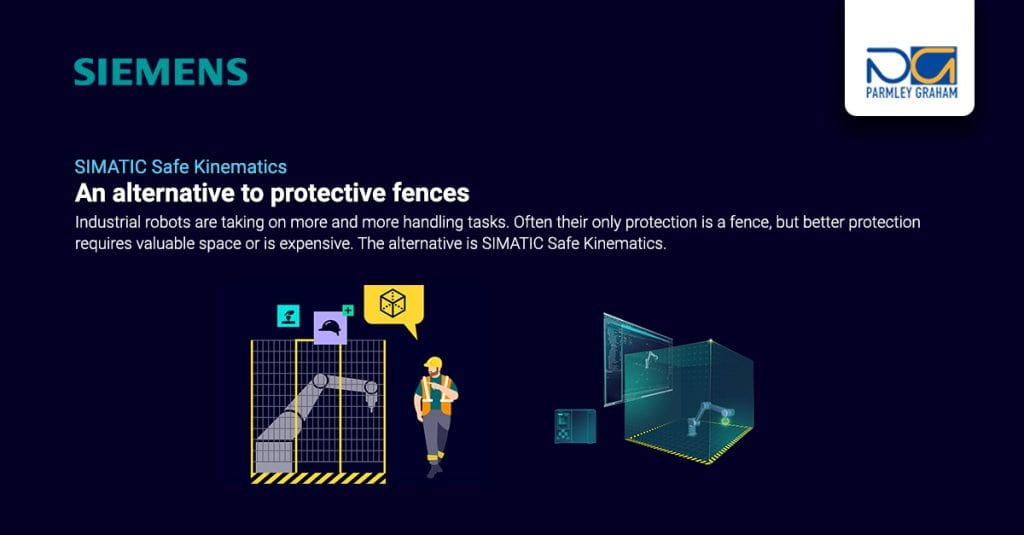
SIMATIC Safe Kinematics for monitoring kinematics in space
SIMATIC Safe Kinematics is an advanced solution from our partner Siemens designed to safely monitor and control kinematic movements within a specified workspace. This technology is particularly useful in applications involving complex machinery and robotics where safety and precision are paramount.
By integrating advanced safety functions into the automation system, industries can protect their workforce, reduce downtime, and maintain compliance with safety standards. Investing in this technology ensures a safer and more productive working environment for complex machinery and robotic applications.
Below is a detailed overview of how SIMATIC Safe Kinematics can be utilised for monitoring kinematics:
Hardware
SIMATIC S7-1500F Controllers
- Fail-safe CPUs: These controllers are designed for safety-related applications and are capable of executing safety programs alongside standard automation tasks.
Safety Modules
- ET 200SP Distributed I/O: Modules with integrated safety functions for decentralised setups.
Drive Systems
- SINAMICS Drives: Provides precise control and safety functions for motors and robotic actuators.
Software
TIA Portal
- Safety Integrated: This tool within the TIA Portal provides a comprehensive environment for programming, configuring, and diagnosing safety applications.
- Safe Kinematics Configuration: A specific part of the TIA Portal for setting up and monitoring safe kinematics.
SIMATIC Safe Kinematics Runtime Software
- Ensures real-time monitoring and control of kinematic movements within defined safe zones.
Benefits
Enhanced Safety
- Compliance with Safety Standards: Ensure compliance with international safety standards (e.g., ISO 13849, IEC 62061) by integrating safety functions directly into the automation system.
- Minimised Risk: Reduce the risk of accidents and injuries by implementing reliable safety measures.
Operational Efficiency
- Real-Time Monitoring: Enable continuous monitoring of kinematic movements to ensure ongoing safety without interrupting operations.
- Reduced Downtime: Implementing safe kinematics reduces the likelihood of accidents, leading to less downtime and higher productivity.
Flexibility and Scalability
- Modular System Design: Easily expand and adapt the system to accommodate new machinery or changes in the production process.
- Seamless Integration: Integrate with existing Siemens automation systems, leveraging the TIA Portal for unified programming and monitoring.
Functionality
Workspace Monitoring
- 3D Workspace Definition: Define safe working areas in three dimensions to ensure that machinery and robots operate within predetermined safe zones.
- Dynamic Monitoring: Continuously monitor the position and movement of robotic arms or other kinematic systems in real-time.
Collision Avoidance
- Safe Position Monitoring: Track the exact position of moving parts to prevent collisions.
- Speed and Distance Monitoring: Ensure that the speed of moving parts is controlled to avoid unsafe interactions.
Safe Stop and Intervention
- Emergency Stop Functions: Implement immediate stop functions if the system detects an unsafe condition or deviation from the safe zone.
- Safe Reduced Speed: Automatically reduce the speed of movements when operators enter predefined safety areas.
Discuss Further
If you wish to explore further how Parmley Graham can help with your automation needs, complete your details and we’ll be in touch:
Access Siemens Example
Industrial Automation
To access the Siemens Example, visit :
To browse our products for industrial automation, visit: