Electronics Manufacturing
Optimising productivity and competitiveness the smart way.
Fast growth, new technologies, short product lifecycles, and high complexity are typical drivers in the Electronics Industry. Product designers, electronics manufacturers, and machine builders alike can benefit from the digital transformation by making good use of the endless data generated in their companies. It’s all possible thanks to Siemens’ Digital Enterprise portfolio, which combines the real and digital worlds and includes smart solutions specifically for the Electronics Industry.
Overview
Taking advantage of simplicity, speed, flexibility, and sustainability.
Whether you’re a product designer, manufacturer, or machine builder, innovation and production cycles have to be kept as short as possible in order for companies in the Electronics Industry to withstand strong competitive pressure. The goal is to bring out new products faster than your competitors. Siemens’ Digital Enterprise portfolio for the Electronics Industry offers you four critical advantages: simplicity, speed, flexibility, and sustainability.
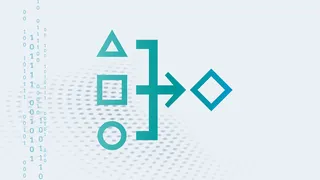
Simplify processes and reduce complexity
Simplify processes and reduce complexity through the seamless, bidirectional transfer of engineering and construction data. You can also configure automation in the TIA Selection Tool and transfer the configuration for technical application to TIA Portal to reduce effort and costs.
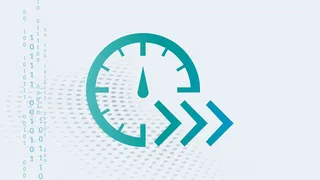
Shorten workflows and time to market
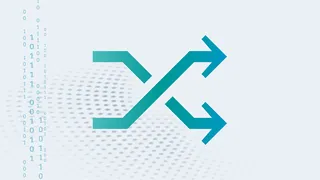
Rely on maximum flexibility
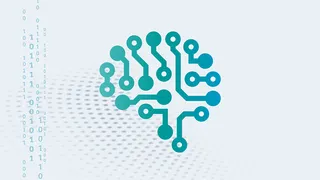
Get ready for the future
Solution
Digital Threads offer solutions specifically for the Electronics Industry
Overcoming challenges – Turning complexity into a competitive edge
Fast and confident decisions with the Digital Enterprise
The Siemens Digital Enterprise portfolio offers product designers, electronics manufacturers, and machine builders the right hardware and software to meet any challenge. In a true Digital Enterprise, the combination of the real and the digital worlds permits seamless integration of the entire value chain, from design to implementation, while a constant flow of data enables ongoing optimisation.
As a means of overcoming challenges, Digital Threads represent a common thread that runs through all the tasks and processes throughout the entire product and production lifecycle. Digital Threads provide digitalised processes and revolutionise the way in which electronic products are developed, produced, and optimised.
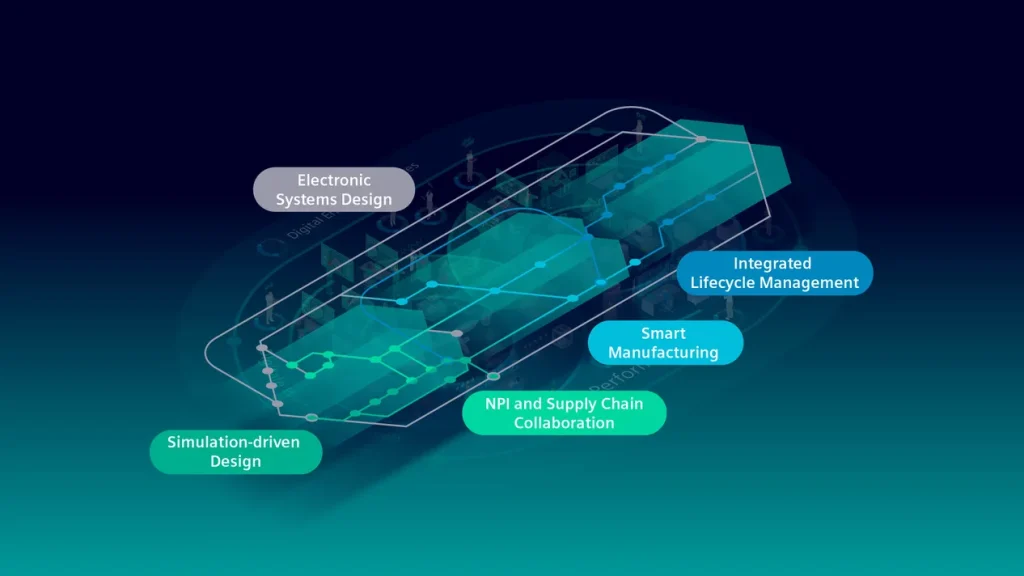
Electronic system design
The development of today’s complex electromechanical products requires seamless collaboration between different disciplines like electrical engineering, electronics, mechanical engineering, simulation, software, and data management.
Multidisciplinary design is based on Siemens comprehensive digital twin. It includes mechanical engineering, electrical engineering, and software in a single collaborative tool and a single environment, permitting the shared use of data and the reuse of existing modules.
Isolated electronic design functions are integrated into a multidisciplinary, collaborative design environment in order to allow simultaneous development and construction by multiple teams in multiple locations. The result is a Shift Left approach that improves efficiency and quality in the early design phases.
Simulation-driven design
Electronic products offer increasingly complex functions that place high demands on reliability. At the same time, these products have to be launched faster than those of the competition while also being fault-free.
By performing simulations and tests using Siemens digital twins, it’s possible to arrive at designs that are right the first time – designs that are digitally optimised and whose performance is pre-analysed.
Company-wide collaboration and the exchange of knowledge, best practices, and results improve the quality and performance of products. High-quality data analyses generate new knowledge for making decisions in real time based on feedback from the digital twin.
NPI and supply chain collaboration
Manufacturers are increasingly dependent on supplier parts and services from around the world. The result is a more complex supply chain that poses tremendous challenges to collaboration and data management throughout the entire product lifecycle.
Openness and communication between OEMs and suppliers is essential for the tight integration and real-time feedback loops that connect people, processes, and data on a global level.
NPI and supply chain collaboration requires that suppliers be integrated in product development early on. It also ensures transparency thanks to the availability of precise supplier information in all departments worldwide and provision of the right information at the right time via secure and efficient data transmission.
Smart manufacturing
Smart manufacturing permits operational data to be fed back into the entire value chain. As a result, product design and production activities are continuously optimised in a closed decision-making process that increases efficiency and shortens the time to market for new products.
This allows you to break down the silos between different process disciplines so that you can achieve a higher degree of workflow automation through digitalisation and increase production efficiency. Thanks to quantitative and qualitative information, you see your business more clearly and are able to make more reliable decisions.
Using synchronised data and analyses, you can detect problem areas that limit productivity and result in failures. At the same time, you gain access to prompt and accurate knowledge so that you can avoid the reliability and safety issues that lead to expensive product recalls and warranty problems.
Integrated lifecycle management
Integrated lifecycle management offers flexibility for adapting to changes in business and meeting all the challenges of product development. Companies can take control of product data and processes using a single information source and optimized processes for managing all aspects of the product, from its design to the end of its service life.
By providing a shared work environment for multiple disciplines with the same requirements, you can immediately and drastically improve quality, increase production quantities, reduce cost overruns, and lower the risks around compliance with specifications.
By linking the technical requirements to the product lifecycle, you allow all participants to make product decisions based on the right, defined requirements.
For your specific requirements, talk to us.
To see how we can help with your systems or if you have any enquiry, please get in touch – we’ll be pleased to help. Send us an email at support@parmley-graham.co.uk or fill the form below.
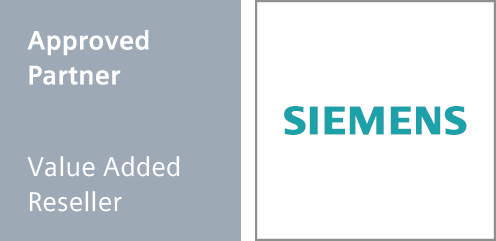
We are Siemens trusted and approved distribution partner.
As a Value Added Reseller in Siemens’ Approved Partner network, Parmley Graham are a proven supplier of a wide range of quality products in the UK and globally.
Find out more how this will benefit you or check Siemens Configurator.